As a manufacturer looking into the Injection Molding Machine Types process, it’s key to know the different THY Precision injection molding machine types. These machines vary, each offering unique benefits for specific production needs. By exploring the wide range of injection molding machines for plastics, you can find the best one for making high-precision parts. But, which Injection Molding Machine Types is the top choice? Let’s dive into the world of injection molding equipment manufacturers to find out which types of plastic Injection Molding Machine Types are best for your business.
Key Takeaways
- Understand the different injection molding machine types available and their specific applications.
- Explore the injection molding machine capacities and specifications to match your production needs.
- Discover the leading injection molding machine suppliers and their offerings.
- Evaluate the injection molding machine prices and consider the benefits of using used Injection Molding Machine Types.
- Determine the best injection molding machine for your high-precision part manufacturing requirements.
Understanding the Different Types of Injection Molding Machine Types
Injection molding machines come in two main types: hydraulic injection molding machines and all-electric injection molding machines. Each type has its own benefits and suits different production needs. It’s important to know the differences to pick the right machine for making precise parts.
Hydraulic Injection Molding Machines
The hydraulic injection molding machine uses hydraulic power for injection force. It needs careful temperature control to avoid waste. Keeping it running smoothly is key to avoid hydraulic system damage from sitting idle too long.
All-Electric Injection Molding Machines
The all-electric injection molding machine costs more at first but has many pluses. It doesn’t have a hydraulic system, so there’s no risk of leaks. Plus, it doesn’t need to be kept in standby or adjusted for temperature, making it more efficient and reliable than hydraulic machines.
Injection Molding Machine Type | Hydraulic | All-Electric |
---|---|---|
Injection Force Source | Hydraulic power | Electrical motors |
Temperature Management | Requires constant monitoring and adjustment | Stable temperature, no need for adjustments |
Efficiency | Moderate | High |
Initial Cost | Lower | Higher |
Liquid Leakage Risk | Present | Eliminated |
When picking between hydraulic injection molding machines and all-electric injection molding machines, think about what you need to produce, your budget, and the details of the parts you’re making. The all-electric option might save money over time, but hydraulic machines are still a good choice for some projects.
Hybrid and Specialized Injection Molding Machine Types
In the world of injection molding machine types, hybrid and specialized models are changing the game. They mix the best of hydraulic and all-electric tech. This creates machines that are efficient, precise, and cost-effective.
The Netstal injection molding machine is a great example of this. It’s a hybrid model that shows off the benefits of combining technologies. It’s efficient and cost-effective, thanks to its smart design.
Another type is the servo oil-electric injection molding machine. It has a high-precision servo motor. This makes it as cost-effective as all-electric machines but better in many ways. It has simpler, more accurate, and durable parts, which cuts down on maintenance costs.
Hybrid and specialized injection molding machine types have more to offer. They can handle higher pressures than all-electric machines. This is a big deal for making precise parts that need top-notch control and consistency.
“The hybrid injection molding machine technology is a game-changer, combining the best of both worlds to deliver unmatched efficiency and cost-effectiveness.”
For companies wanting to lead, checking out hybrid and specialized injection molding machine types is key. These advanced machines bring new levels of precision, efficiency, and savings. This can help your business succeed in the tough manufacturing world.

Material-Specific Injection Molding Machine Types
Choosing the right injection molding machine depends on the material you work with. At THY Precision, we know how different materials need different machines. We offer thermoplastic injection molding machines, thermoset plastic injection molding machines, and powder metal injection molding machines for your needs.
Thermoplastic injection molding machine types are versatile and efficient. They work with materials that can be melted and reused, reducing waste. But, these parts might not last as long or handle heat well. They also might not be as precise as thermoset parts.
Thermoset plastic injection molding machines are for materials that can’t be melted again. They make parts that last a long time and are very precise. But, they can’t change mold designs easily and take longer to cure than thermoplastics.
Powder metal injection molding machines mix metal powders and binders to make precise metal parts. They’re great for complex shapes but are limited by the materials used and cost.
Injection Molding Machine Type | Material | Advantages | Limitations |
---|---|---|---|
Thermoplastic | Thermoplastics | High production efficiency, easy reuse | Limited durability, lower precision |
Thermoset | Thermosets | High durability, exceptional precision | Limited flexibility in mold design, longer curing time |
Powder Metal | Metal powders and binding agents | High precision, complex shapes | Limited material availability, higher initial cost |
At THY Precision, we have many injection molding machine types for your needs. Our team can help you pick the best machine for your project. We ensure your parts are top quality and perform well.
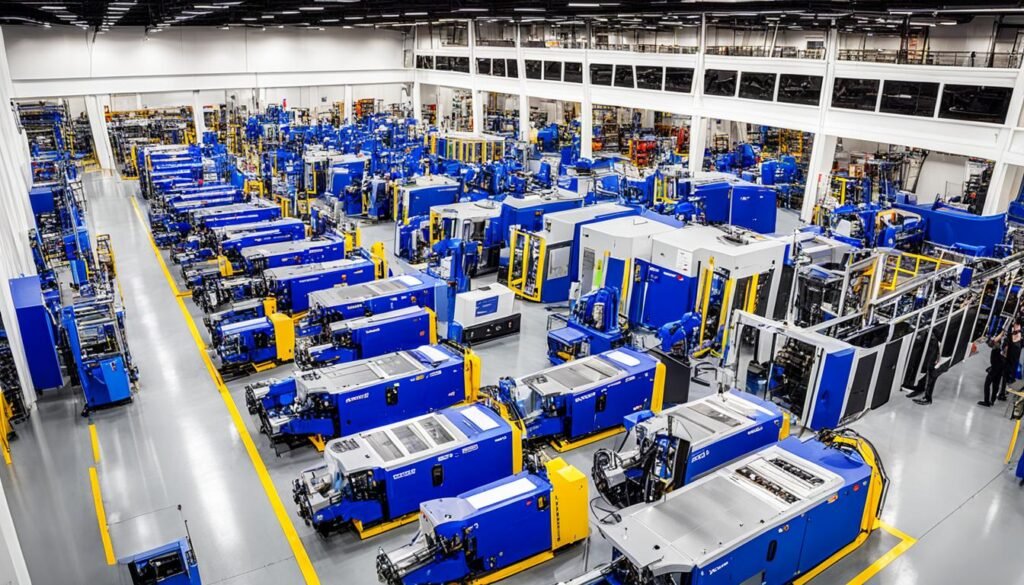
Advanced Injection Molding Machine Technologies
Advanced technologies are changing how we make high-precision parts in injection molding. We now have single-cylinder, double-cylinder, and four-cylinder machines. There are also toggle type, multi-color, and tie-bar-less machines. This industry has seen a big change in recent years.
Single-cylinder, double-cylinder, and four-cylinder machines use different numbers of cylinders for high pressure. They are great for many applications and are very precise. But, they use more energy and cost more to maintain.
Toggle type machines use a special mechanism for high clamping forces. They work faster than old hydraulic machines. But, they cost more to start and use more energy, so they’re best for specific needs.
For making complex, multi-color, and multi-component products, the multi-color machine is perfect. It has multiple units and molds for complex designs. This makes assembly cheaper but costs more to start and needs more upkeep.
The tie-bar-less machine design is a big leap in injection molding technology. It removes tie-bars, making the machine smaller and allowing the mold to open fully. This means better efficiency, easier mold changes, and more automation.
Machine Type | Key Features | Advantages | Considerations |
---|---|---|---|
Single-cylinder, Double-cylinder, and Four-cylinder Direct Pressure Injection Molding Machines | Use different numbers of cylinders to achieve high injection pressure | Offer high injection pressure and wide range of applications | Higher energy consumption and maintenance costs |
Toggle Type Injection Molding Machines | Use a toggle mechanism to create high clamping force | Provide high clamping force and faster cycle time than hydraulic machines | Higher initial cost and energy consumption than electric machines |
Multi-color Injection Molding Machines | Use multiple injection units and molds to create multi-color and multi-component products | Suitable for complex shapes and designs, reduces assembly cost | Higher initial cost and more complex operation and maintenance |
Tie-bar-less Injection Molding Machines | Eliminate tie-bars for a smaller machine footprint and allow the mold to be placed on the entire platen face | Increased efficiency, easier mold change and maintenance, improved automation capabilities | Requires specialized design and engineering |
The injection molding industry is always getting better. These new technologies are making it possible to make parts with more precision. By knowing what each machine can do, manufacturers can make smart choices. This helps them improve their processes and lead the way.
Conclusion
Choosing the right injection molding machine types is key for high-precision molding. Each type, like hydraulic, all-electric, hybrid, and specialized, has its own benefits. These benefits affect the quality and precision of your molded parts.
Things like temperature control, injection pressure, and speed matter a lot. Also, the materials used and how well the mold is maintained are crucial. They help ensure your parts are accurate, consistent, and of high quality.
At THY Precision, we know how important injection molding machine types are for making high-precision parts. Our experts can help you pick the right machine for your needs. With the right machine, process settings, and mold care, we can make sure you get the quality parts your industry needs.
Boost your injection molding machine types performance and improve your high-precision parts. Contact THY Precision today. Let us show you how our skills can upgrade your manufacturing.